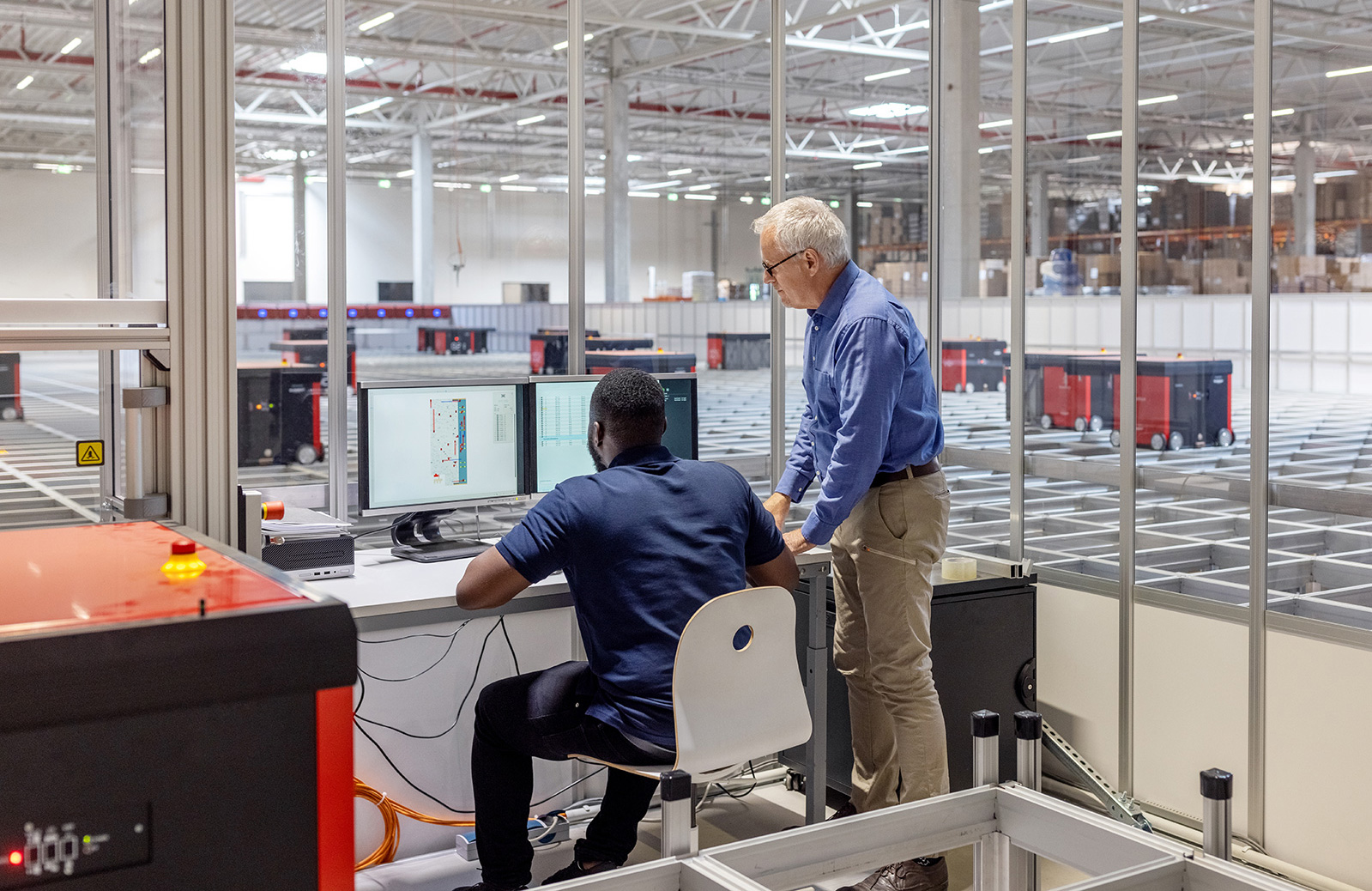
Definition of the Kanban Board
The Kanban board (visual label or panel in Japanese) is a just-in-time production management system. It prioritizes workflow regulation based on demand, just-in-time production, and work-in-progress visualization.
A Pragmatic Approach to Business Management
The Kanban approach was initially introduced by Taiichi Ohno, the director of Toyota, in the 1950s. David J. Anderson, a project management expert, later formalized the Kanban approach for intellectual work.
This method adopts the principles of software development, product management, and IT. It is a simple management system that allows:
- Eliminating waste;
- Visualizing the production flow;
- Limiting work in progress.
With this method, you can improve team collaboration and optimize the quality of your products.
A Solution to Optimize Workflow Management
Dynisco, a leader in plastic material extrusion, implemented an automated Kanban inventory system. This approach allowed them to reduce active stock by 40% across all their facilities.
At MWT Sourcing, we support businesses in the procurement process. You can entrust us with production, quality control, and international shipping of your products. We ensure that your production chain complies with standards. Feel free to conduct a factory audit with our customized solution.
What Are the Principles of the Kanban Method?
This method is based on four fundamental principles that promote continuous improvement. It differs from the Scrum method, which relies on fixed-duration sprints in an iterative work environment.
Start with What You Are Currently Doing
The Kanban method integrates with existing processes while respecting established practices. You can identify strengths and areas for improvement in your factory without disrupting its current organization. Employees can learn to follow the ongoing workflow and handle real-world challenges.
Embrace Gradual Changes
This management method focuses on the progressive improvement of business processes. Teams should adopt a continuous optimization approach by implementing gradual changes.
Respect Current Processes, Roles, and Responsibilities
This principle is based on respecting the existing roles, personnel, and skills within your company. The Kanban system makes existing processes more efficient without replacing them.
Encourage Leadership at All Levels
Every worker, regardless of their position, can be a leader in implementing and managing the Kanban system. You should encourage individual responsibility and initiative-taking.
How to Apply the Kanban System in a Factory?
The Kanban method operates on the pull flow principle. You must adapt it to your factory’s operations to achieve optimal results.
Visualizing the Workflow
Visualization is the foundation of the Kanban methodology. You must identify bottlenecks and track progress in real time.
The Kanban card is at the heart of this production system. It consists of visual signals that guide teams’ work throughout the production flow. Each board represents a work unit or task to be completed.
You can then create a diagram with columns for each step of the process. Kanban boards provide a global view of the ongoing workflow. The Kanban card must be moved as work progresses.
Our approach to the Kanban system helps visualize the workflow and automate task tracking. This will help improve the efficiency of your production plant.
Limiting Work in Progress
Set strict limits on the number of ongoing tasks at each stage of the process to maintain a smooth workflow. Limiting work in progress (WIP) also helps prevent work overload and ensure the quality of finished products.
Training Teams in the Kanban Method
Monitor the progress of ongoing tasks or items through the production process.
Workflow management ensures that tasks move predictably through the board. You can then define rules and policies governing the workflow, which should be communicated across all workstations.
Train your team to master the production system developed by Toyota. Team members should report issues they encounter for immediate resolution.
Implementing Feedback Loops
Feedback loops detect problems, introduce adjustments, and maintain clear communication.
Conduct daily meetings and thorough Kanban board reviews to adjust production processes.
The Agile approach also promotes a collaborative culture at all levels of your company. However, it is essential to understand the challenges of the Kanban method and learn how to overcome them. MWT Sourcing is available to support your efforts!